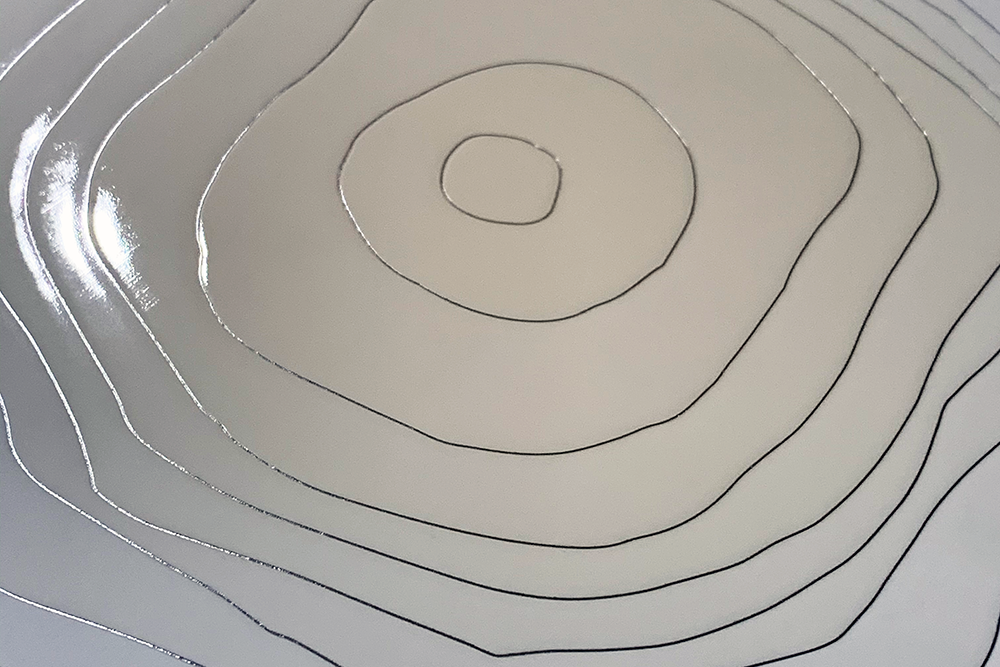
厚盛り印刷を重ねてみる
一般的に厚盛り印刷とは、透明な樹脂インクをUV(紫外線)を照射する事により、インクを隆起した状態で硬化させる加工を言いますが、一度硬化させた厚盛りインクの上に、更に厚盛りをすることは可能なのでしょうか?
またそれにより、どのような表現が可能なのでしょうか。
本実験では厚盛り印刷の多層刷り試してみました。
今回はテスト用に下記のようなデータ(A)を準備致しました。
左上の一番大きな絵柄(1層目)から、右下の一番小さな絵柄(9層目)まで順に重ねて厚盛り印刷をしていきます。
9層の地層の様なイメージです。
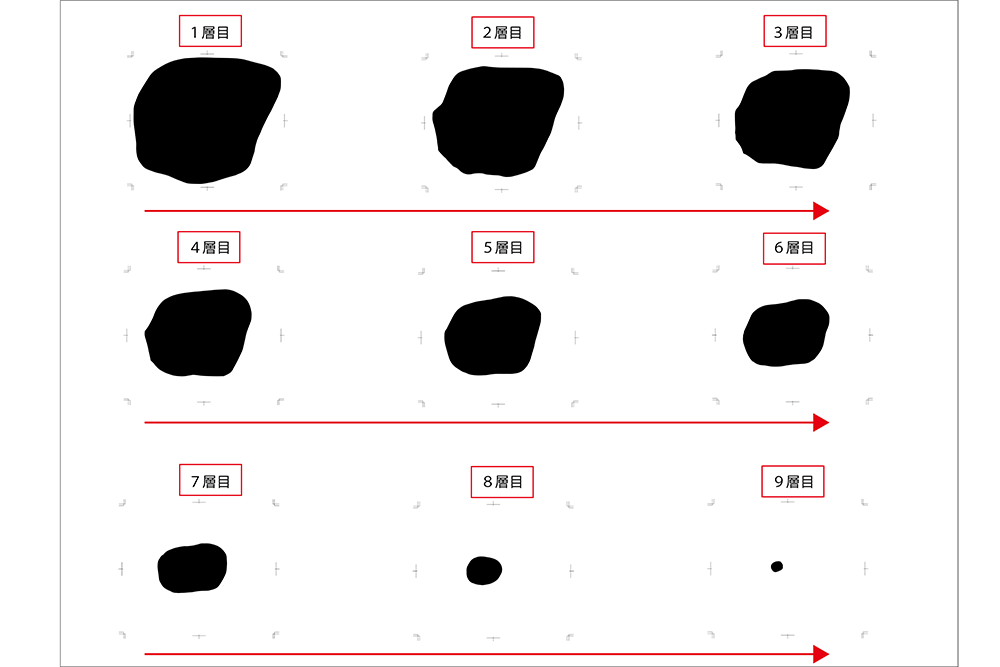

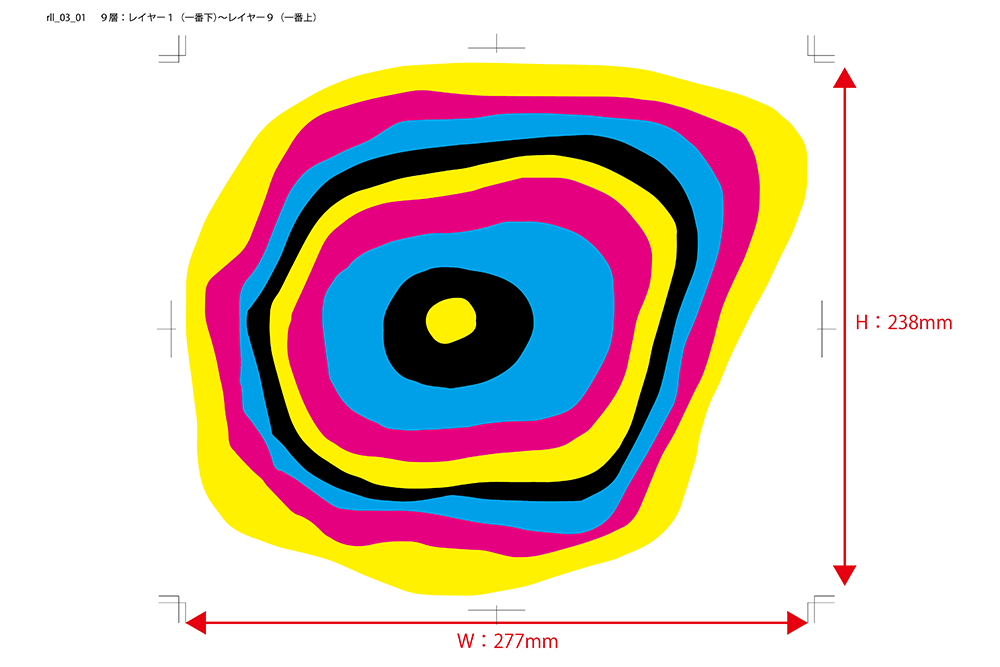
データ(B)上では便宜上CMYKで色分けしておりますが、データ(A)の9種のデータを重ねたイメージです。透明な樹脂インクの厚盛りがこの様な層状に重ねてプリントされて行きます。
尚、今回は株式会社セントラルプロフィックス様にご協力頂き、デジタルで厚盛りプリントが可能なインクジェジェット(swissQprint製Impala Ⅱ)を使用してテスト致します。
厚盛りの多層プリント実験結果
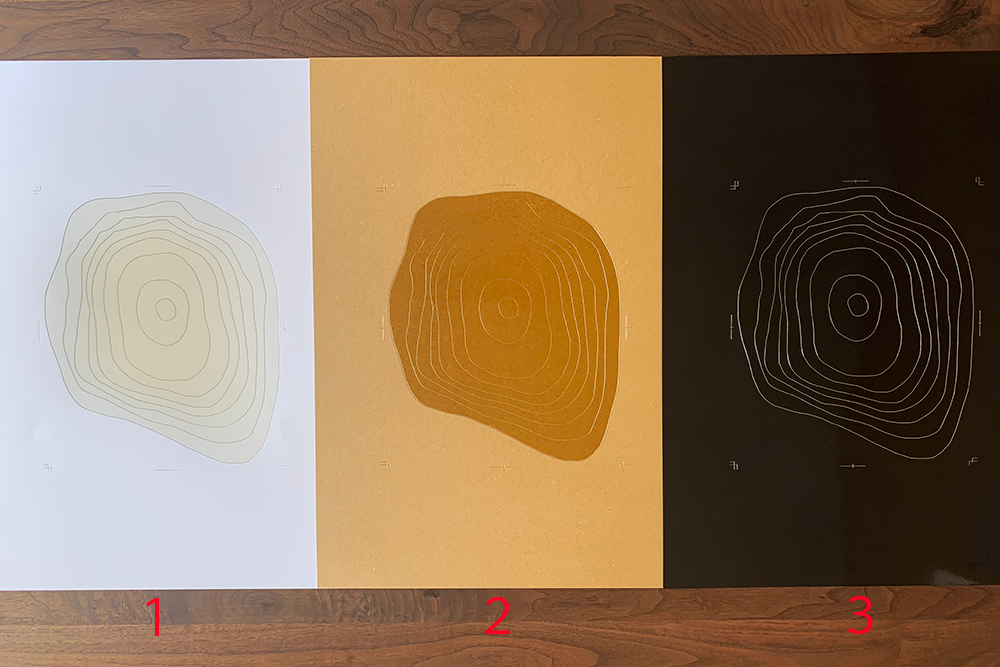
今回は用紙を上記画像の3種でテストしてみました。
左より
No,1:ヴァンヌーボV(スノーホワイト)46Y/275kg
No,2.:GAファイル(キャメル)46Y/450kg
No,3:カラーグロリア ブラックA 46T/28kg
下記それぞれの結果です。
(*1〜9層の各データの境界線は印刷する用紙にシルバーでラインを入れてあります。)
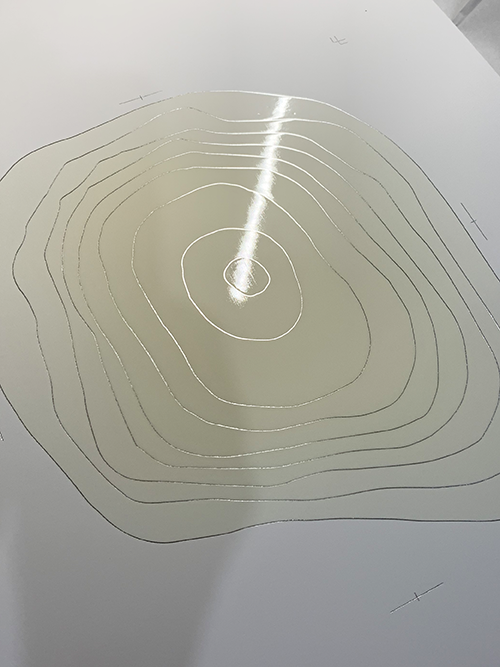
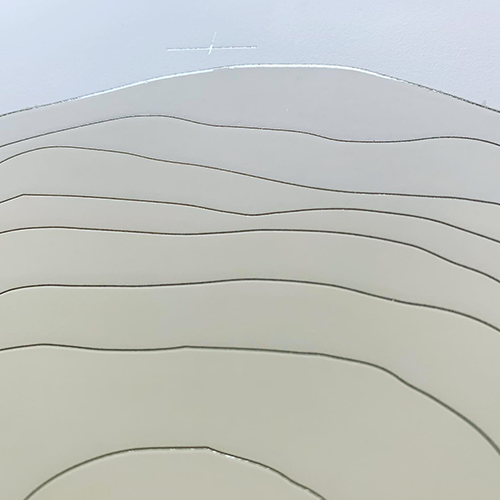
ヴァンヌーボは紙肌に柔らかい質感を持った用紙ですが、印刷適性の高い塗工処理を用紙表面にしてあるため、厚盛りの表面の光沢もきれいに再現されます。
尚、用紙色が白と言うこともあり、中心に向かい樹脂の重なりが多くなるほど透明度が落ち乳白色になって見えます。
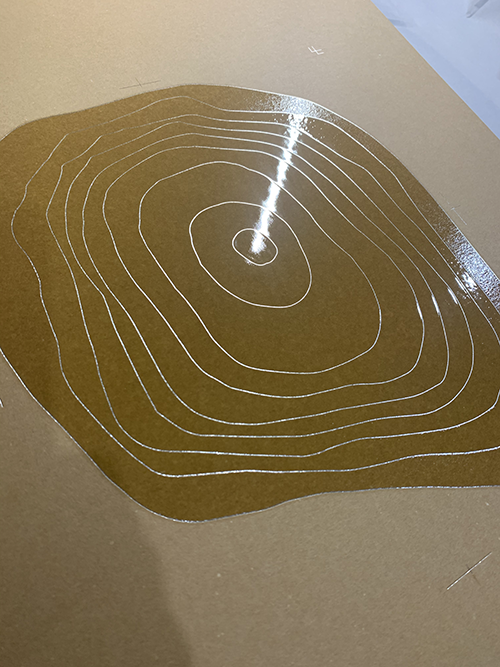
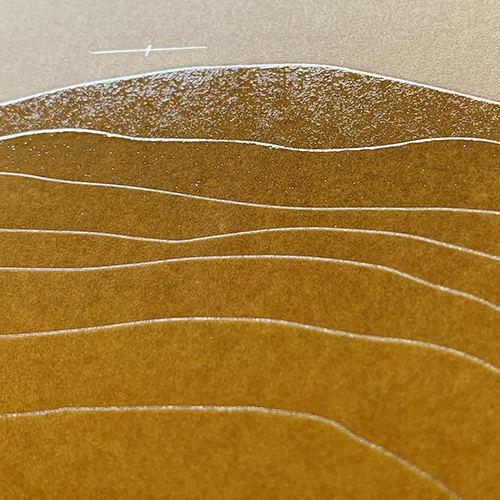
続いてNo,2のGAファイルですが、こちらはNo,1のヴァンヌーボのような塗工が施されていないので、樹脂インクが用紙に吸われ気味になります。
特に一番外側の第1層目はインクが吸われ、表面がザラザラしています。2層目以降、徐々にインクが重なることにより表面の表情がフラットになってきます。今回の実験では一番、層ごとの表面の表情に違いが見れました。
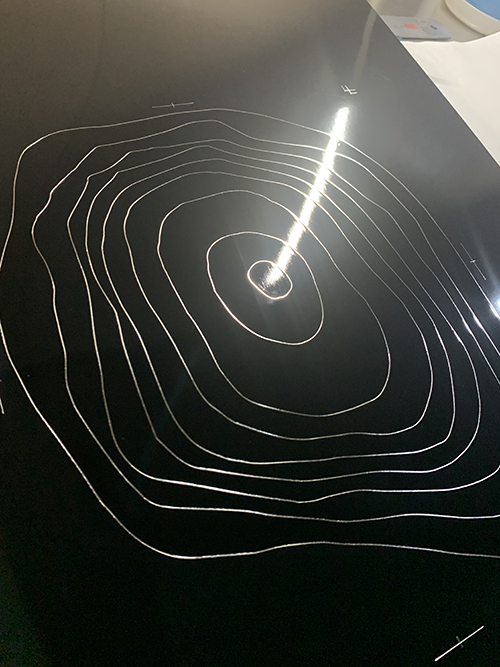
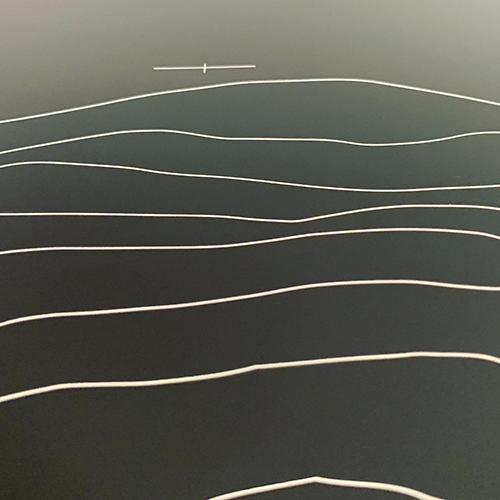
最後はカラーグロリア(ブラックA)です。こちらは元々黒い用紙の表面にプレスコートがされており鏡面仕上げの用紙です。厚盛りインクの表面は3種の用紙の中で最もフラットに再現されますが、その分逆に紙の鏡面に馴染んでしまい視覚的効果は薄いです。
厚盛りを9層重ねたがインクの盛り上がり感は・・・
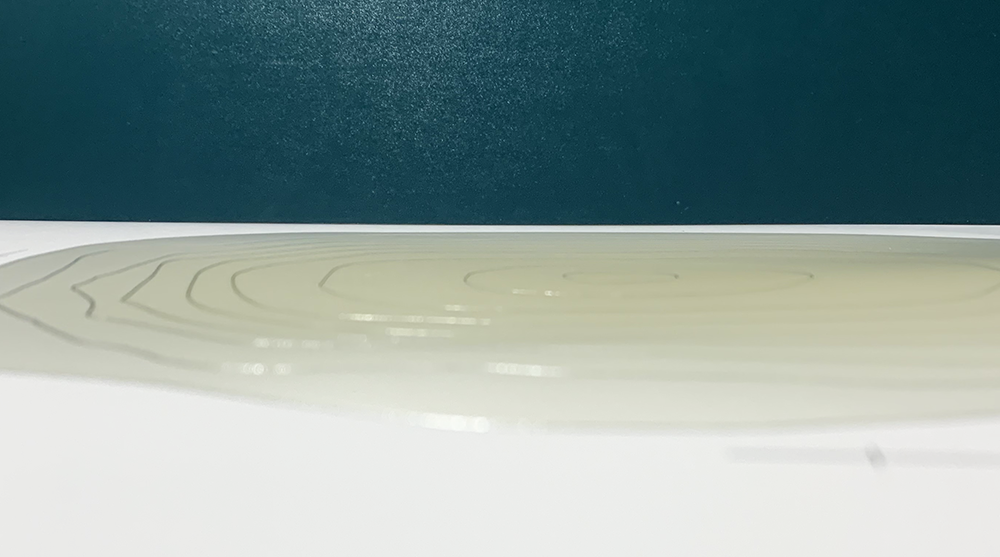
先に厚盛り部分の表情に関しては記載しましたが、実は9層も樹脂インクを重ねたのにそんなに被膜の高さは感じられません!
少しは山のような形状になるかと思いましたが・・・。
早速、実際に厚みを測ってみました。
ヴァンヌーボV(スノーホワイト)46Y/275kgの実測値で
・印刷なし(用紙自体)の厚み:約0.45mm
・一番外側(1層目)の厚み:約0.48mm
・一番内側(9層目)の厚み:約0.82mm
1層目と9層目の差は0.34mm程度の厚みです。
各層のインクジェットの吹き付け被膜を測ると約0.03〜0.04mmぐらいで確かに9層重なっているのですが目視的には分かりづらいです。
それはどうしてでしょうか。
厚盛り印刷を重ねても高さが出ない理由

上記(図1)は1層だけ印刷した厚盛りインキを横から見たイメージです。
面積が広い厚盛りは中央部分に近づくにつれインク(樹脂)がヒケのように凹んでしまいます。
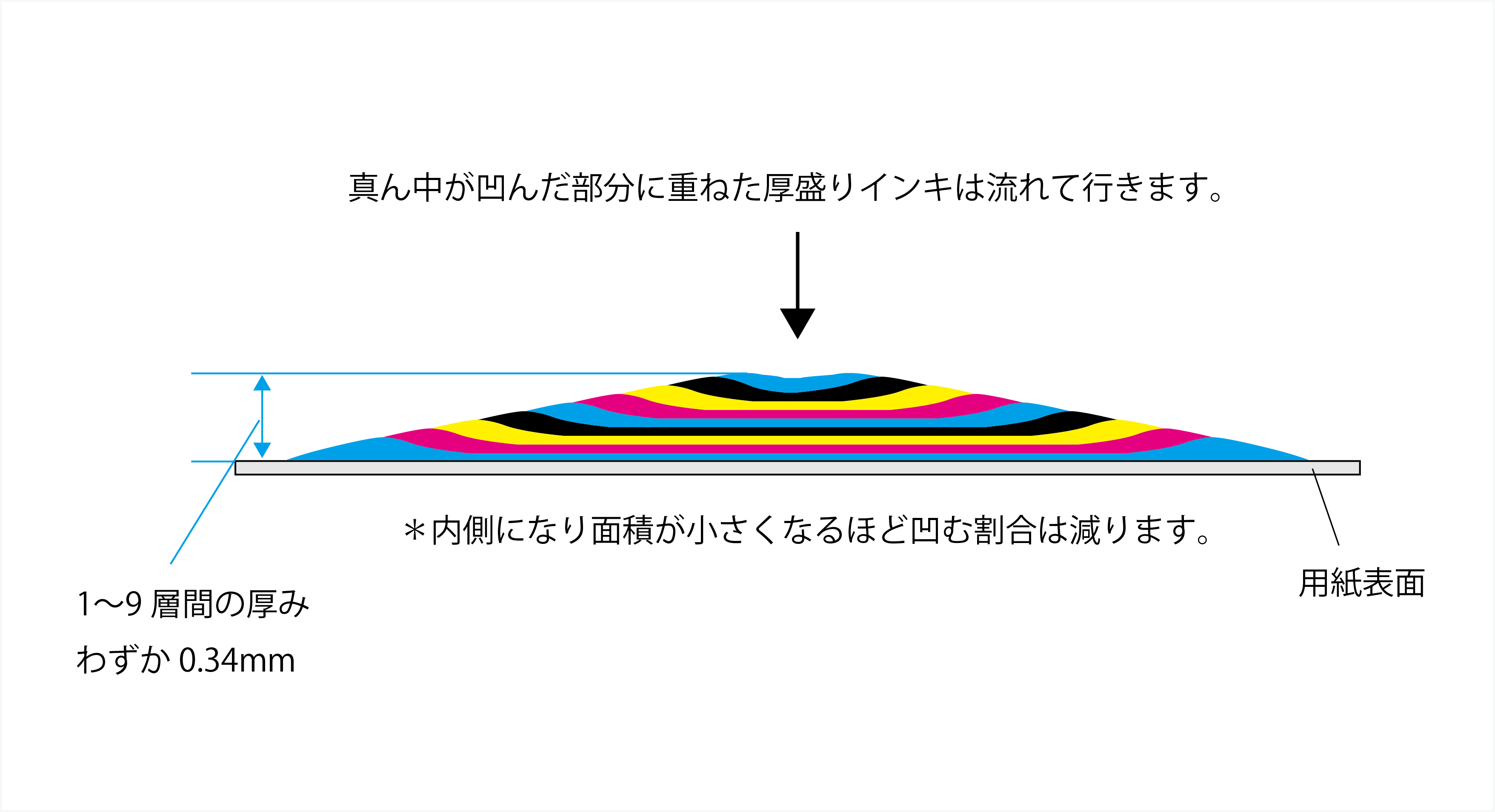
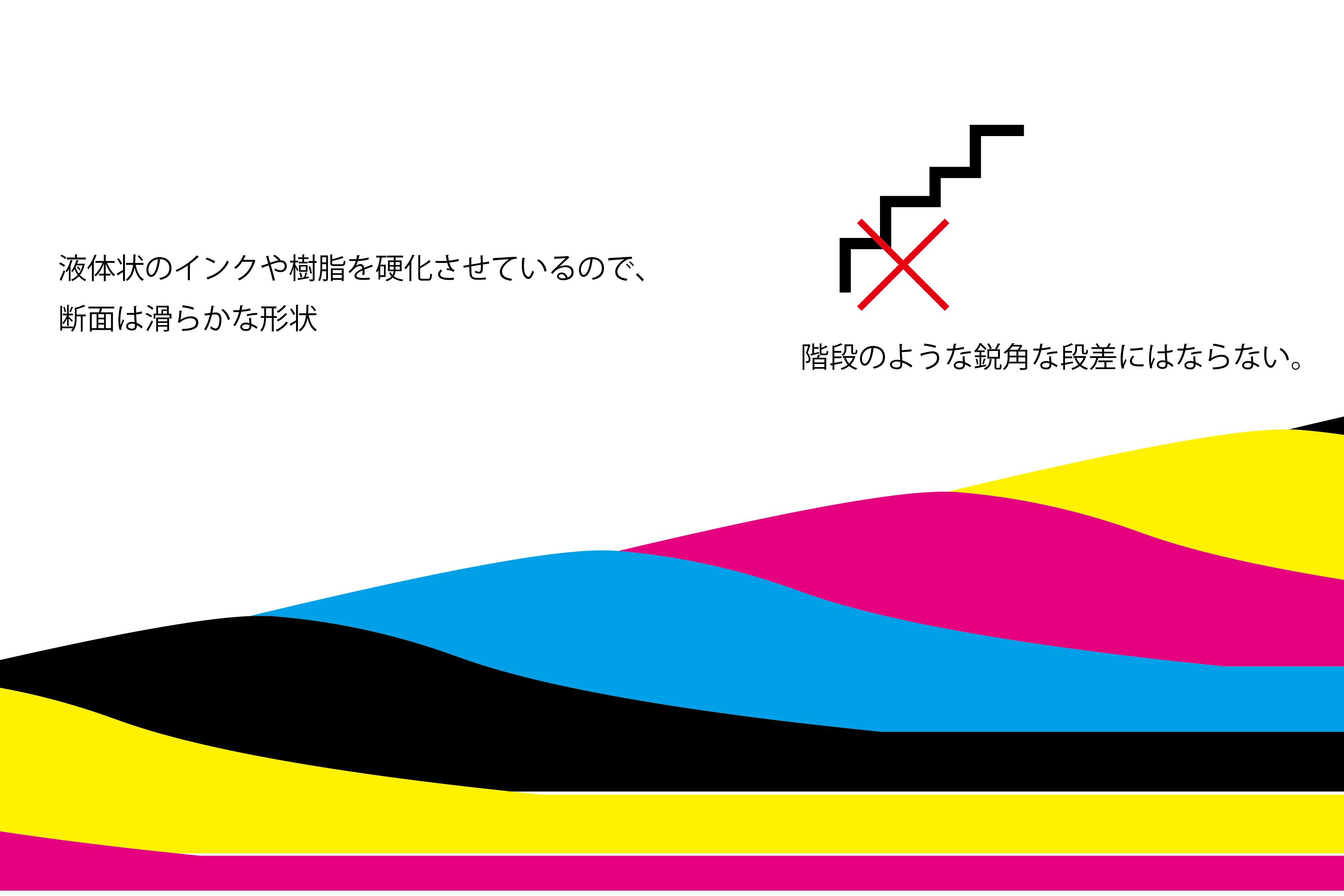
図2は厚盛りを9層重ねた場合を横から見たイメージです。
2層目以降重ねていく厚盛りインクも同様に、中央は凹んでしまいます。
お皿を重ねていくようねイメージですね。
厚盛り印刷はUV(紫外線)でインクや樹脂を速乾させる技術ですが、やはり液体の流れは多少なり発生します。
また、図3の拡大イメージのように各層の断面もけっして鋭角な訳ではなくなだらかな形状なので、段差が目視では認識しづらいです。
しかも1〜9層間のわずか0.34mmの厚みの中での段差なのですから尚更です。
上記の理由から厚盛り印刷では面積が広い絵柄を重ねていっても、視覚的効果は低いものとなりました。
今回はインクジェットの厚盛りプリントでの検証でしたが、シルクの厚盛り印刷でも同じ症状は発生します。
厚盛りを重ねる表現は、薄く敷いたベタ面にライン状などの面積のない絵柄を乗せる2層刷り程度が現実的のようです。画像では分かりづらいのですが一応参考画像掲載しておきます。

以上、長くはなった割りに視覚効果的には低いものとなってしまいましたが、一度多層刷りのテストはしてみたかったので実行してみました。
好結果ばかりが表現の可能性を広げる訳では無いと思いますので、今回の実験もこれはこれで意味はあったと思います。
またこれからも気になった手法はチャレンジして行きたいと思います。
ではでは。